Builders Fee & Tactics to make money
BUILDERS FEE & STRATEGIES TO MAXIMISE EARNINGS THROUGH DESIGN AGREEMENT ALTERATIONS
We deemed it valuable to compile a frequent list of excuses builders commonly use. Addressing these excuses can be somewhat tiresome when clarifying to homeowners that these issues are not unique to their project but are encountered across various projects we handle. It seems like a tactic employed by builders, expecting it to go unnoticed or unchallenged, ultimately benefiting the builder by saving substantial amounts of money.
CATALOGUE OF COMMON STRATEGIES BUILDERS UTILISE TO CUT COSTS AND PRIORITISE PERSONAL GAINS
If you’re a homeowner navigating through your project and your builder has raised any of the following points from the list below, we’ve compiled the most probable explanations for their inquiries. Over the years, we’ve encountered and cataloged all the excuses builders employ to take shortcuts, ultimately enhancing their profits at the expense of quality workmanship. The primary motivation behind these suggestions is to maximize earnings, while the secondary reason may involve a reluctance to adhere to correct building methods or a lack of experience to execute the works in compliance with building regulations. Any builder proposing the following before taking on a project should be approached with caution. The examples below illustrate a few instances of excuses commonly used by builders to evade the proper execution of the job.
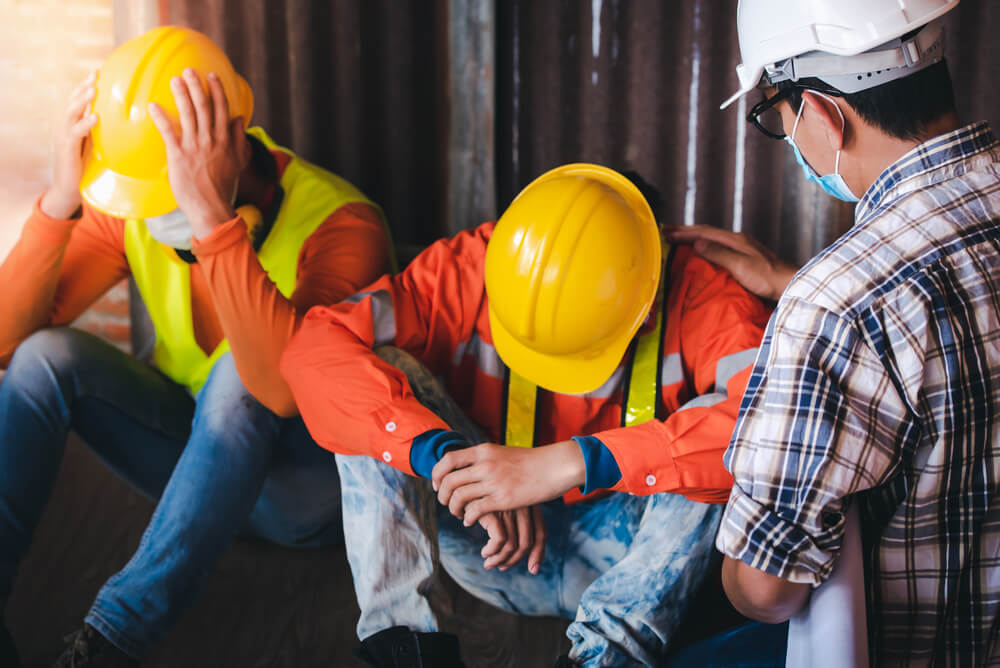
AVOID BECOMING A TARGET OF THESE WIDESPREAD STRATEGIES.
Guidance: No, it’s not feasible to use a single beam. The engineer has devised a box frame comprising 4 STEELS to be securely bolted together, addressing the extra loading and providing lateral restraint. This specialized design has been approved by building control and involves 2 columns, 1 ground beam, and 1 upright.
Savings:
The potential cost savings by avoiding the purchase and installation of 4 STEELS (BOX-FRAME) would be approximately £5000+vat.No, it’s not advisable. The Engineer has crafted a new foundation with distinct dimensions in width and depth, tailored to endure the loading requirements of the new design. The existing foundation is insufficient in size and lacks the requisite structural composition to withstand the loading of the new structure.
Savings:
Avoiding excavation and the use of cubic meters of concrete presents significant cost savings in labour, and skip hire costs would be approximately £250 per cubic meter.No, it’s not recommended. The post on the drawings is specifically designed as a solidly fixed steel post, secured to two beams with bolts. This design involves fixing one end of the post in the floor beam and the other end in the ridge beam, offering a robust steel fixing arrangement, considered the best method for loft conversions. Timber and steelwork have limited fixture results.
Savings:
Although using a timber post simplifies fabrication detailing, welding on-site, and installation due to easy on-site cutting and fixing, it only provides limited structural support. The potential cost savings would be around £350+vat.No, it’s not advisable. Brickwork or blockwork is considerably stronger than a timber wall, especially since the ridge beam relies on the gable wall for support. Opting for a timber wall is a shortcut involving less robust and more expensive materials, eliminating the need for a bricklayer. A timber wall lacks the same properties as a solid wall in terms of thermal composition, durability, fire protection, soundproofing, and aesthetic appeal.
Savings:
While using timber materials and carpentry skills may offer cost savings of around £1000+vat, it compromises the structural integrity and overall quality of the loft construction.No, it’s not recommended. The Engineer has meticulously designed the structure, supported by thorough calculations, ensuring the capability to withstand all loadings on the new structure. Strict adherence to the design is imperative.
Foregoing a steel beam or column might seem like a cost-saving measure, but it comes with potential consequences.
Savings:
The savings could be around £300+vat per meter, but it compromises the structural integrity of the new construction.No, it’s not advisable. The client has selected specific sizes and quantities of skylights, which have already gained approval from the local authority. The chosen sizes are crucial for bringing in natural daylight into the loft space. After investing over £40,000+vat in their loft conversion, the client wouldn’t want a dark loft room.
Savings:
While opting for MK04 Velux instead of MK06/8 might offer cost savings of £150 – £250 for each Velux, it compromises the client’s original design preferences and the overall lighting quality in the loft space.No, it’s not recommended. The client has deliberately chosen brickwork, aligning with strict council design guidelines. Brickwork not only offers a more aesthetically pleasing finish compared to a blockwork render but is also maintenance-free. Deviating from the chosen brickwork to blockwork would compromise the design integrity and visual appeal.
Although switching to blockwork may reduce construction costs substantially, it contradicts the client’s preferences and the established design guidelines for the extension.
No, it’s not advisable. The design has been meticulously crafted to meet specific U-Values, particularly in light of recent changes to Approved Building Regulation documents, specifically Part L since June 15th. Adhering to the specifications outlined in the drawings is crucial for the homeowner to secure a final completion certificate of compliance.
Savings:
Opting for thinner insulation is a common but risky tactic to cut corners, hoping it goes unnoticed by inspectors. However, inspectors are vigilant and aware of such tactics, often requiring builders to expose other areas of the wall to verify proper insulation installation. While using 100mm Kingspan or Celotex insulation instead of 50mm may save the builder around £75+vat per sheet, it jeopardizes the compliance and overall energy efficiency of the construction.No, it’s not advisable to proceed without confirming planning permission. All design works, regardless of falling within Permitted Development, should be reviewed by planners for peace of mind. No design is deemed secure until a submission is made, and a final certificate of a planning decision is obtained. Despite the builder’s eagerness to start immediately, they lack planning expertise. A breach in planning control could result in the builder disappearing, leaving the homeowner to navigate the aftermath.
Our motto in the office is “NO DESIGN IS LAWFUL UNTIL PROVEN BY MEANS OF A SUBMISSION.” With 32 Boroughs in London, each planning system may interpret PD legislation differently. Assuming a design falls under PD is a risky gamble, as a case officer may interpret guidelines differently, leading to a refusal. Building without proper certification could invite Enforcement, resulting in significant financial loss.
Initiating works without necessary certification, such as planning permission or a certificate of lawfulness, is solely the homeowner’s responsibility. For a mere £103 and an 8-week wait, obtaining a certificate of lawfulness allows a council planner to check the design for compliance. If planning permission is needed, the process involves paying £206 and waiting 8 weeks for a decision.
No, it’s not recommended. The engineer has specifically designed the project using steel beams, and adherence to the provided drawings is crucial. Timber, with its different properties compared to stainless steel, weighing up to 90KG per meter, is not a suitable alternative. It’s essential to follow the specified drawings without any deviations.
Builders may suggest doubling up on timbers to cut costs, especially if they haven’t initially priced the job with steel beams. However, attempting such a substitution could lead to additional expenses later on. Steel beams and columns, while more expensive, are integral to the structural integrity of the project, ensuring safety and compliance with engineering standards.
No, raising the ridge of the house is generally not allowed under permitted development, and obtaining planning permission for such changes is rare, as it alters the street scene in the council’s perspective.
It’s crucial not to heed builders suggesting the idea of raising the ridge or extending further. Any alterations to extend outward or raise the ridge line risk putting the homeowner in breach of planning control, making them solely responsible for potential consequences.
No, it’s not recommended. If builders include this service, it’s essential to verify that the application has been properly registered. Some cases have seen inspectors not conducting necessary on-site inspections, putting the final build at risk of not receiving a completion certificate.
Avoiding payment for building control services might save the builder approximately £1000+vat, but this could jeopardize the homeowner’s experience, as witnessed in a few instances last year. It’s crucial to ensure all necessary inspections and certifications are carried out for a compliant and secure construction process.
No, it is not permissible. Builders must have engineering drawings with calculations for steel connection detailing before ordering or installing any steel beams or columns. This rule is well-known and universally understood. Guesswork by builders often results in inaccuracies, causing issues when building control requests engineering calculations. The engineer’s solution may differ, leading to complications and extra costs for the homeowner.
Some builders may try to avoid hiring an engineer to save money, assuming they won’t be asked for calculations by inspectors. However, inspectors eventually uncover these shortcomings. Investing in proper engineering calculations, which typically cost around £100+vat per beam or column element, is essential to avoid complications and ensure a successful construction process.
No, it is not acceptable. A reputable builder, when providing a quote, should request and review structural calculations to ensure accurate pricing, including beam sizes and connection details. Pricing a job without a complete design is unprofessional and can lead to significant issues. Homeowners may initially receive a quote, compare it with others, and later discover that the builder demands additional funds upon realizing incomplete or updated structural designs. This situation can cause panic and disruptions to the project.
Builders who claim that structural calculations should be included in the design are misinformed. The homeowner typically pays separately for engineering calculations, conducted by an experienced engineer, not the architect. If a builder fails to notice missing beam sizes or connection details on the drawings, it’s their responsibility. Homeowners should ensure these elements are in place before starting any project, as the design must be checked for compliance by the building inspector before work commences or materials are purchased.
Are you facing issues with your builder’s practices? Seek advice from Kun Arch.
Yes, if you encounter any problems with your builder, consult the building control department, particularly Kun Arch. Your assigned inspector ensures the project proceeds reasonably, free from shortcuts. Inspectors, familiar with various tactics, swiftly respond to calls, often conducting site inspections within 24 hours of booking.